When Compliance Isn’t Enough: Ensuring Compliance Through Alternative Methods Under the OHSA
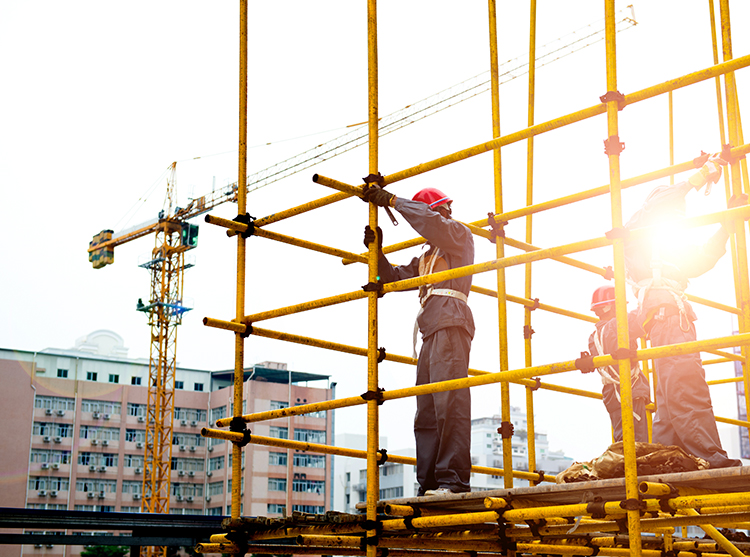
The Occupational Health and Safety Act (OHSA) creates a framework for achieving worker safety in Ontario. Its provisions impose general duties on the people who work at the workplace, and its regulations list specific technical steps that must be taken to protect worker safety. For example, the Construction and Industrial Regulations each respectively speak to listed requirements of what must be done on construction projects and in factories.
However, an interesting case from the Court of Appeal makes it clear that simply complying with the regulations isn’t always enough. The regulations don’t provide prescriptive certainty, and employers must meet the higher standard of taking all reasonable precautions to protect their workers. The case is Ontario (Labour) v. Quinton Steel (Wellington) Limited.
What happened? A worker fell from a temporary welding platform that was less than three metres high. He died. The platform wasn’t protected by guardrails, and the worker wasn’t wearing fall arrest equipment. However, even though neither protection was required by the applicable regulation, and even though the employer had met all of the listed requirements that had been set for the work by that regulation, the Ministry of Labour still charged the employer under the OHSA with failing to take all reasonable precautions to protect the worker.
At trial, the employer argued that the applicable regulation created a comprehensive and discrete code for the protection of workers in this situation, and that its compliance with that code was the end of the matter. The trial Justice agreed. So did the first appeal Judge.
However, when the matter got to the Court of Appeal, the panel disagreed. It found that the regulations cannot foresee every situation, and that there may be reasonable steps that have to be taken for the protection of workers outside of those that are contained in the regulations. In other words, there may be times when complying with the regulations just isn’t enough.
Why is this case important? Sometimes, the off the rack approaches that are set out in the regulations just don’t fit. In those cases, employers need to understand not only that customized solutions may be necessary, but that they are allowed. The regulations speak to this1 and the Court of Appeal, through this case – by recognizing that the regulations don’t create exclusive, complete and discrete codes – arguably has confirmed it.
Continuing with that line of thought, we know from experience that most employers are extremely hesitant to deviate in any way from the regulations, and we also recognize that many employers have real difficulty understanding that there are situations in which they may have to go beyond the onerous requirements that have been set out in the regulations.
However, what the Quinton Steel case demonstrates is that worker safety is the standard that has to be met. The rules that are set out in the regulations may reflect an attempt to achieve worker safety, but they do not set or change the standard, nor can they be used to justify an employer’s conduct that falls short of the standard.
Given that, we recommend that employers take the following three steps when they are looking to apply the regulations to their workplaces:
Step 1: Employers should always start by assessing their operations and by asking whether the requirements prescribed by the applicable regulation provide enough protection for their workers. For example, in the Quinton Steel case, the regulations did not require any fall protection where workers were working on temporary platforms that were less than three metres off the ground. However, the risk of falling still presented a danger and, arguably, other reasonable precautions could have been taken. The take-away is that one should never look at the regulations as the gold standard. In reality, they reflect a minimum standard.
Step 2: Employers should next ask whether the prescribed requirements are actually unsafe in light of a workplace’s unique environment or operations. For example, section 26.3 of the Construction Regulation provides that where there is an open hole through which a worker can fall more than 2.4 metres, a protective covering or guardrails should be installed. However, depending on how the worksite is configured, those protections could pose trip hazards and create more danger than they protect. In such circumstances, if alternative precautions are more appropriate, they should be used, and the workers and the Joint Health & Safety Committee should be notified of the variance.
Step 3: Before adding to, or deviating from, a prescribed requirement, an employer should always consult with a subject matter expert. If, god forbid, there is a workplace incident, an employer needs to be able to demonstrate that they considered the issue and consulted with the appropriate people before doing anything. Accidents are always unintended. However, if one happens at your workplace, you want to be able to show not only that it was unintended, but also that (a) it couldn’t reasonably be anticipated, and (b) you did everything you could to protect against it. Consulting with a subject matter expert can go a long way in doing that.
1 Section 2 of the Industrial Regulation permits varying the composition, design, size and arrangement of any material, object, device or thing prescribed by the regulation so long as the variance provides factors of strength, health and safety that are equal or greater to the factors of strength, health and safety found in the prescribed requirement. Section 3 of the Construction Regulation has a similar provision, but adds a requirement that written notice of the varied procedure be given to the employer’s Joint Health & Safety Committee, or health and safety representative.